Take you to know
What is Powder coating and surface modification production line
The powder coating and surface modification production line is also named as powder modification machine,powder surface modifying machine / equipment,mineral powder Coating machine / equipment, which is mainly responsible for three purposes, the first is mixture, the second is dispersion and third is surface modification to the powder via a specified melting modifier, resulting in a good combination. It can be divided into continuous modified production technology and batch ones, also there are two combinations of processes.
Industrial basic technical requirements:
- Dispersity of modifier is increased by means of dilution, emulsification and spray.
- The material to be modified is fed into the coating machine, where the material will be mixed, dispersed and then coated by atomizing modifier sprayed by dosing pump and the the powder will be coated evenly and completely.
- Control of system temperature and time is so regulated not only to meet the requirement for coating mechanism or modifier on technical conditions, but also to guarantee coating reaction or coating sufficiency.
- The coordination of feeding material and modifier ensure the complete coating.
- In conjunction of accessories ( depolymerizing machine or classifier), the product quality will be improved largely.
- We achieve the highest coverage or modification with minimal coating material or cost
- Surface modification has important practical significance for improving the performance of powder, improving its practical value and developing the application field.
- In polymer materials, composite materials such as plastics, rubber, adhesives, etc., non-metallic powders must be modifieds a filler ,Such as calcium carbonate, kaolin, talc, quartz, wollastonite, asbestos, magnesium hydroxide, aluminum hydroxide, etc,to enhance their compatibility with the matrix, dispersion, mechanical strength and overall performance.
- Surface modification is one of the necessary processing means for the filler to change from general incremental filler to functional filler. It is also the main purpose of surface modification of mineral filler.
- The main effects of surface modification of mineral powder fillers include dispersion, viscosity reduction, filling, interface mechanics.
- The most commonly used powder modification methods are surface chemical modification method, coating modification method, mechanical force chemical modification method.
- According to the characteristics of the modified materials, continuous production process or batch production process can be selected.
- There are many options for modifying equipment
- The modifier can be selected from stearic acid or a coupling agent (titanate coupling agent, aluminate coupling agent, phosphate coupling agent, etc.)
- Wide application, can achieve the desired activation effect on various inorganic mineral powders.
- Dispersity of modifier is increased by means of dilution, emulsification and spray.
- The material to be modified is fed into the coating machine, where the material will be mixed, dispersed and then coated by atomizing modifier sprayed by dosing pump and the the powder will be coated evenly and completely.
- Control of system temperature and time is so regulated not only to meet the requirement for coating mechanism or modifier on technical conditions, but also to guarantee coating sufficiency.
- Ensure the adequacy of material coating by uniform feeding and coordination with the quantitative feeding of modifiers
- In conjunction of accessories ( depolymerizing machine or classifier), the product quality will be improved largely.
- After modification, the powder has various functions such as dispersion, viscosity reduction, filling, interface mechanics.
- Personalized solution for powder surface modification based on material properties and product use
Process and Equipment
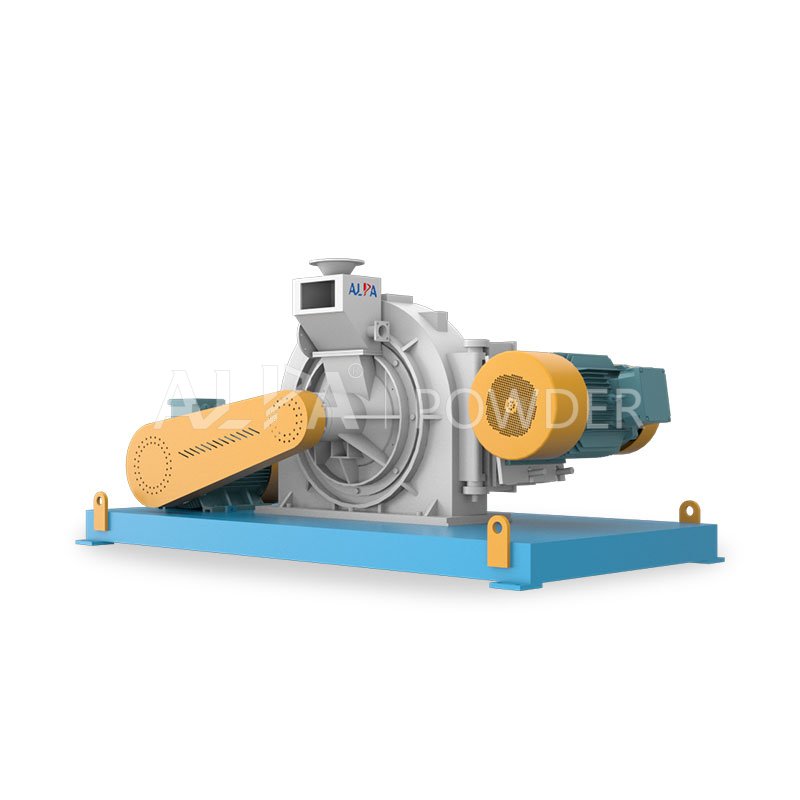
Pin Mill Coating Machine
- Normally, this type is very popular in European and American markets.
- Two rotors running in opposite direction, their linear speed can be up to 200m/s
- High-speed impact, shear and friction lead to full dispersion of materials and temperature rise, resulting in powder modification completely.
- We achieve the highest coverage or modification with minimal coating material and cost
- In polymer materials, composite materials such as plastics, rubber, adhesives, etc., non-metallic powders must be modified as a filler to enhance their compatibility with the matrix, dispersion, mechanical strength and overall performance.
- The modifier can be selected from stearic acid or a coupling agent (titanate coupling agent, aluminate coupling agent, phosphate coupling agent, etc.)
- Wide application, can achieve the desired activation effect on various inorganic mineral powders.
- Dispersity of modifier is increased by means of dilution, emulsification and spray.
- The material to be modified is fed into the coating machine, where the material will be mixed, dispersed and then coated by atomizing modifier sprayed by dosing pump and the powder will be coated evenly and completely.
- Control of system temperature and time is so regulated not only to meet the requirement for coating mechanism or modifier on technical conditions, but also to guarantee coating sufficiency.
- Ensure the adequacy of material coating by uniform feeding and coordination with the quantitative feeding of modifiers
- In conjunction of accessories ( depolymerizing machine or classifier), the product quality will be improved largely.
- After modification, the powder has various functions such as dispersion, viscosity reduction, filling, interface mechanics.
- The whole system is easy to operate, high degree of automation, high efficiency, low cost.
- Personalized solution for powder surface modification based on material properties and product use
Three-Roller Coating Machine
- It is very popular in China
- Realize powder surface modification by changing inner vortex with three rotating rotors
- High speed friction spontaneous heat, Low investment and operation cost without any additional heating system.
- We achieve the highest coverage or modification with minimal coating material and cost
- In polymer materials, composite materials such as plastics, rubber, adhesives, etc., non-metallic powders must be modified as a filler to enhance their compatibility with the matrix, dispersion, mechanical strength and overall performance.
- The modifier can be selected from stearic acid or a coupling agent (titanate coupling agent, aluminate coupling agent, phosphate coupling agent, etc.)
- Wide application, can achieve the desired activation effect on various inorganic mineral powders.
- Dispersity of modifier is increased by means of dilution, emulsification and spray.
- The material to be modified is fed into the coating machine, where the material will be mixed, dispersed and then coated by atomizing modifier sprayed by dosing pump and the the powder will be coated evenly and completely.
- Control of system temperature and time is so regulated not only to meet the requirement for coating mechanism or modifier on technical conditions, but also to guarantee coating sufficiency.
- Ensure the adequacy of material coating by uniform feeding and coordination with the quantitative feeding of modifiers
- In conjunction of accessories ( depolymerizing machine or classifier), the product quality will be improved largely.
- After modification, the powder has various functions such as dispersion, viscosity reduction, filling, interface mechanics.
- The whole system is easy to operate, high degree of automation, high efficiency, low cost.
- Personalized solution for powder surface modification based on material properties and product use

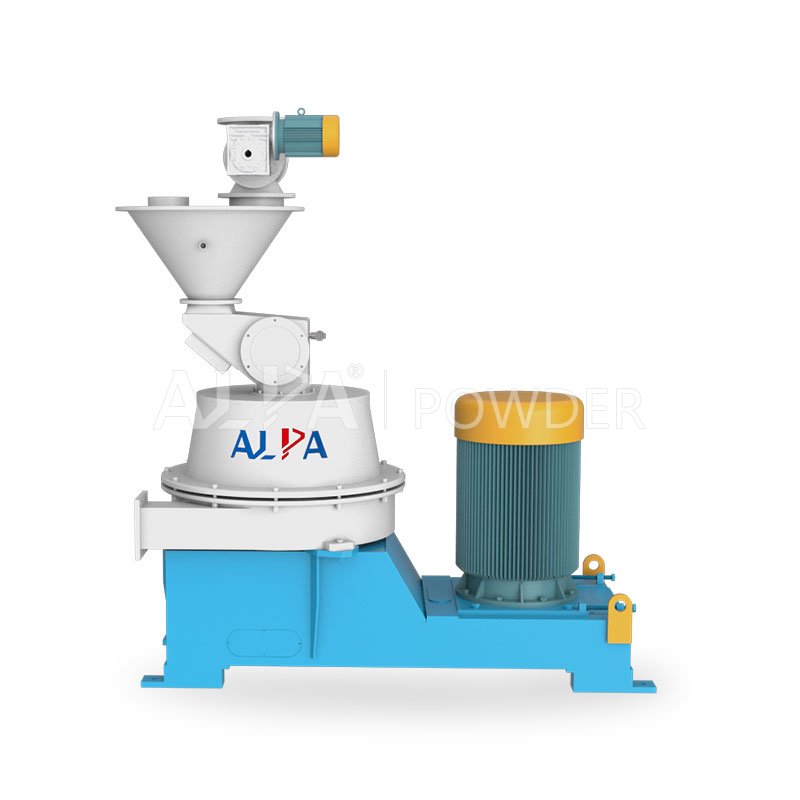
Vortex mill Coating Machine
- The powder coating machine employs conic rotor and stator, the gap between them can be adjusted.
- The highest linear speed of the rotor can reach 130 m / s
- The powder surface modification will be completed by high-speed impact, shear and friction of materials between stator and rotor driven by a motor.
- We achieve the highest coverage or modification with minimal coating material or cost
- In polymer materials, composite materials such as plastics, rubber, adhesives, etc., non-metallic powders must be modified as a filler to enhance their compatibility with the matrix, dispersion, mechanical strength and overall performance.
- The modifier can be selected from stearic acid or a coupling agent (titanate coupling agent, aluminate coupling agent, phosphate coupling agent, etc.)
- Wide application, can achieve the desired activation effect on various inorganic mineral powders.
- Dispersity of modifier is increased by means of dilution, emulsification and spray.
- The material to be modified is fed into the coating machine, where the material will be mixed, dispersed and then coated by atomizing modifier sprayed by dosing pump and the the powder will be coated evenly and completely.
- Control of system temperature and time is so regulated not only to meet the requirement for coating mechanism or modifier on technical conditions, but also to guarantee coating sufficiency.
- Ensure the adequacy of material coating by uniform feeding and coordination with the quantitative feeding of modifiers
- In conjunction of accessories ( depolymerizing machine or classifier), the product quality will be improved largely.
- After modification, the powder has various functions such as dispersion, viscosity reduction, filling, interface mechanics.
- The whole system is easy to operate, high degree of automation, high efficiency, low cost.
- Personalized solution for powder surface modification based on material properties and product use
High-speed mixing coating machine
- Batch-type operation
- Some materials has to be modified by silane coupling agent under high temperature and long time reaction
- Equipped with heating timing device, the modification temperature and time can be controlled.
- Selectable ceramic liner is free from metal pollution, Especially suitable for surface modification of quartz powder.
- We achieve the highest coverage or modification with minimal coating material and cost
- In polymer materials, composite materials such as plastics, rubber, adhesives, etc., non-metallic powders must be modified as a filler to enhance their compatibility with the matrix, dispersion, mechanical strength and overall performance.
- The modifier can be selected from stearic acid or a coupling agent (titanate coupling agent, aluminate coupling agent, phosphate coupling agent, etc.)
- Wide application, can achieve the desired activation effect on various inorganic mineral powders.
- Dispersity of modifier is increased by means of dilution, emulsification and spray.
- The material to be modified is fed into the coating machine, where the material will be mixed, dispersed and then coated by atomizing modifier sprayed by dosing pump and the the powder will be coated evenly and completely.
- Control of system temperature and time is so regulated not only to meet the requirement for coating mechanism or modifier on technical conditions, but also to guarantee coating sufficiency.
- Ensure the adequacy of material coating by uniform feeding and coordination with the quantitative feeding of modifiers
- In conjunction of accessories ( depolymerizing machine or classifier), the product quality will be improved largely.
- After modification, the powder has various functions such as dispersion, viscosity reduction, filling, interface mechanics.
- The whole system is easy to operate, high degree of automation, high efficiency, low cost.
- Personalized solution for powder surface modification based on material properties and product use
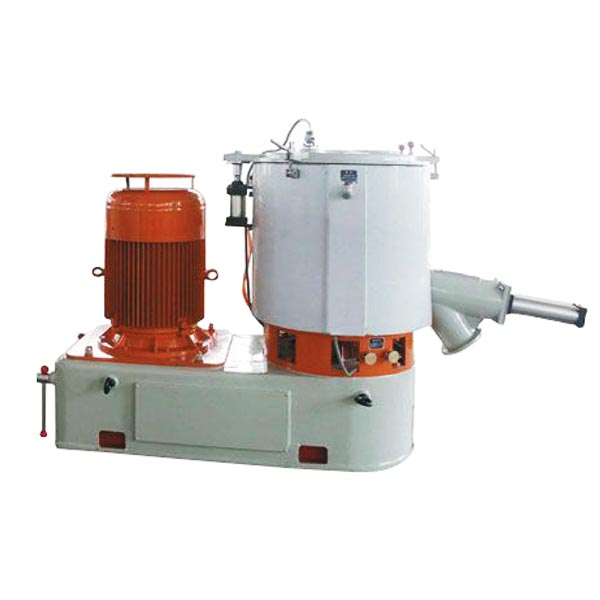
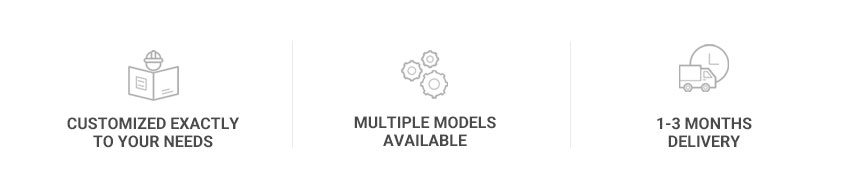
“I don’t know how to choose the best for me.”
IT DOESN’T MATTER
LET US HELP YOU!
The raw material and the particle size, output, and application industry of the finished product determine the choice of equipment and process. As an expert, you will not be unfamiliar with this.If you have any questions, don’t worry, please leave us a message, or “Live Chat” in the lower corner of this page, or contact us via our phone or email.
ANY QUESTIONS OR DEMANDS
PLEASE CONTACT US RIGHT NOW!
Learn More & Get Quotation
Please tell us your needs.
Our engineer will send you solutions and quotes for free.
Or email